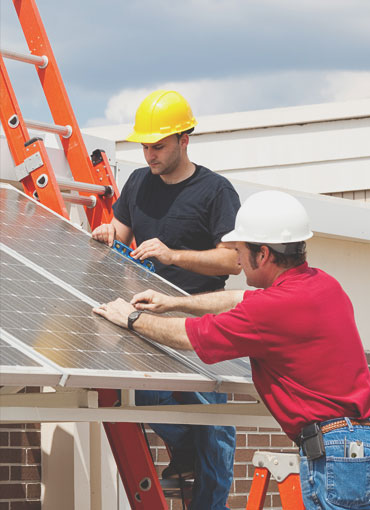
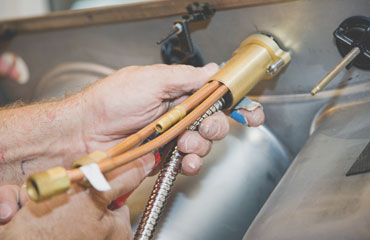
Purpose & Scope
The purpose of this quality plan is to define specific key requirements related to quality performance and ensures a thorough understanding of such by all project parties concerned.
Through PQP awareness and implementation the performance of the engineering, procurement construction and support functions may effectively and efficiently achieve their objectives and provide the Client with a project that fulfills their quality requirements and expectations.
The PQP is supplemental to Electco Quality Management System (QMS) and provides the mechanism to link specific requirements of the Client / project to those of Electco quality system.
And ensuring that these related activities are planned implemented and controlled, and their progress and effectiveness is monitored.
The above summarized and referenced key activities are further expanded upon within the following Key Activities.
Key Activities and Output
Necessary project planning and controls shall be established as part of the developed Electco.
Quality Management System and as appropriate the quality plan refers to this documentation under the key activity headings within this section.
Mobilization
Mobilization is defined as the period starting from contract award and continuing until all Construction is completed.
Engineering
Review of contract drawings, specifications obtain / provide clarifications, coordinate among all related disciplines and produce shop drawings within performance parameters.
Key activities and controls to be established are listed below:
- Shop Drawings
- Production program
- Organization of engineering personnel
- Identification, notification and implementation of changes
- Drawing submittal
Procurement and Material Management
To prepare technical packages comparisons for permanent materials and to secure competent and reliable sources for procurement.
Key activities and controls to be established are:
To develop planning schedules, monitor, accommodate changes and report progress.
Key activities and controls to be established are:
Execute the construction program within the set performance parameters defined by approved shop drawings, approved material submittals and approved quality controls. Key activities and controls to be established are:
Coordination of Major Subcontractors and Specialists
Co-ordination of technical matters, material procurement deliveries to site, and site progress.
Key activities and controls to be established are:
To carry out the QC activities required for achieving compliance with defined plans and specifications through the organization of respective works on site and monitoring quality activities.
Key activities and controls to be established are:
Monitor, administer and protect the Company's contractual and financial relationship with client, consultant, subcontractors and suppliers.
Key activities and controls to be established are:
> Variations arising during the preparation of shop drawings.
> Changes in the scope suppliers /subcontractors /specialist work.
> Request for clarification.
> Meetings with the client.
> Corrective actions identifying errors or omissions in the contract documents.
> Formal notification from the employer.
Document Control
Electco Research & Development Department and associated processes and procedures will as appropriate be utilized to develop and implement the following controls:
Receive, store, protect and distribute materials as required by construction.
Key activities and controls to be established are:
. Ensure permanent materials are acceptable prior to release for site use.
. Status recording and reporting of materials arrival and notification to concerned construction team.
. Upon delivery of material at site the following initial verification will be carried out:
> Inspection of delivery documentation against the Purchase Order
> Checked for quantities under, over and obvious damage
> Notification to site QC for inspection
> Computer data entry in store receiving system
. The issuance of material shall be made on request and warehouse records and computer data base updated accordingly:
> Stores receiving voucher (SRV)/Material Receiving Report (MRR)
Quality Assurance> Site request to stores
> Store Issue Voucher (SIV)
> Materials /services acceptance
> Weekly permanent materials report
> Reconciliation of as-‐‑built quantities and material wastage
To carry out the quality assurance activities required for achieving compliance with defined plans, manuals, processes, procedures, and method statements.
Key activities and controls to be established are:
To provide a wide variety of administrative services to the project, including the maintenance of personnel files, handling and storage of consumable materials related to administrative services.
Key activities and controls to be established are:
• Transfer of employees between projects
• Personnel evaluations